Thick Wall Alloy Tube
Alloy pipes have a hollow section and are used in large quantities as pipelines for conveying fluids, such as pipelines for conveying oil, natural gas, gas, water and certain solid materials. Compared with solid steel such as round steel, alloy steel pipe is lighter when the bending and torsion strength is the same. Alloy steel pipe is a kind of economical cross-section steel, which is widely used in the manufacture of structural parts and mechanical parts, such as oil drill pipes and automobile transmission. Axes, bicycle frames and steel scaffolding used in building construction, etc. The use of alloy steel pipes to manufacture ring parts can increase the utilization rate of materials, simplify the manufacturing process, save materials and processing man-hours, such as rolling bearing rings, jack sleeves, etc., which have been widely used in steel pipe manufacturing. Alloy steel pipes are also an indispensable material for various conventional weapons. Gun barrels and barrels are all made of steel pipes. Alloy steel pipes can be divided into round pipes and special-shaped pipes according to different cross-sectional area shapes. Since the circle area is the largest under the condition of equal circumference, more fluid can be transported by the circular tube. In addition, when the ring section is subjected to internal or external radial pressure, the force is relatively uniform. Therefore, most of the steel pipes are round pipes.
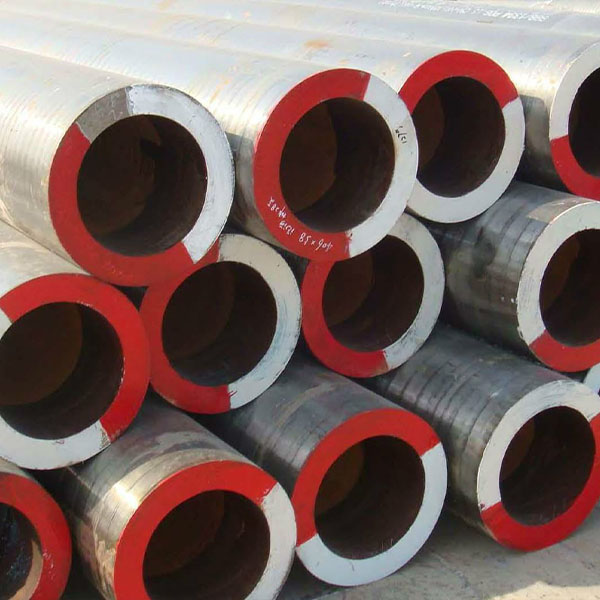
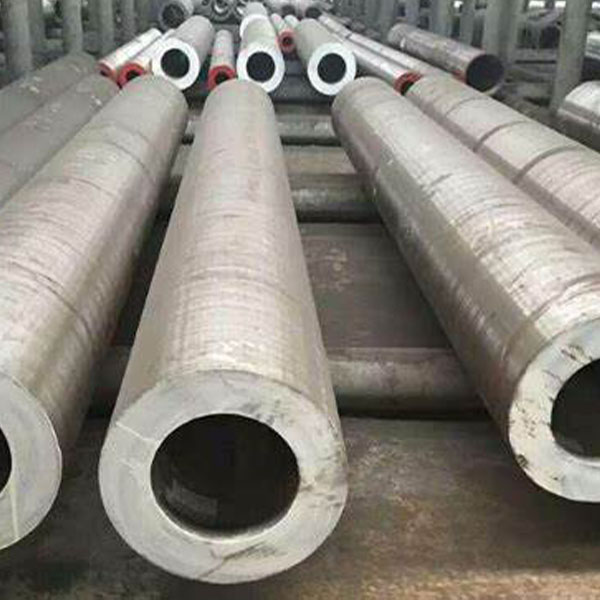
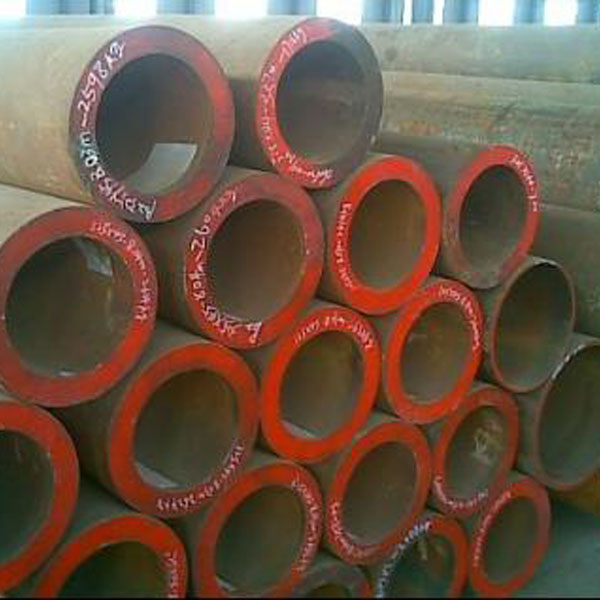
Classification of thick-walled alloy pipes
The biggest advantage of thick-walled alloy pipes is that they can be recycled 100%, which is in line with the national strategy of environmental protection, energy saving, and resource saving. The national policy encourages the expansion of the application areas of thick-walled alloy pipes.
Process overview
Hot rolling (extruded seamless steel tube): round tube billet → heating → piercing → three-roll cross rolling, continuous rolling or extrusion → tube removal → sizing (or reducing) → cooling → billet tube → straightening → water pressure Test (or flaw detection) → mark → warehousing.
Cold drawn (rolled) seamless steel pipe: round tube billet → heating → piercing → heading → annealing → pickling → oiling (copper plating) → multi-pass cold drawing (cold rolling) → billet tube → heat treatment → straightening → Water pressure test (flaw detection) → mark → warehousing.
1XXX alloy series based on pure aluminum.
2XXX Aluminum alloy with copper as the main alloying element.
3XXX Aluminum alloy with manganese as the main alloying element.
Titanium alloy tube use: Titanium alloy tube is mainly used in aviation. It is a kind of alloy tube specially used for aviation with high hardness and high temperature resistance.
4XXX Aluminum alloy with silicon as the main alloying element.
5XXX Aluminum alloy with magnesium as the main alloying element.
6XXX Aluminum alloy with magnesium and silicon as the main alloying elements.
7XXX Aluminum alloy with zinc as the main alloying element.
Alloy tube weight formula: [(outer diameter-wall thickness)*wall thickness]*0.02483=kg/m (weight per meter)