Pipe Flange System
Piping flange refers to the flange used for piping in the pipeline installation, and refers to the inlet and outlet flanges of the equipment when used on the equipment. There are holes on the flanges, and bolts make the two flanges tightly connected. The flanges are sealed with gaskets. The flange is divided into threaded connection (threaded connection) flange, welding flange and clamp flange. Flanges are used in pairs, wire flanges can be used for low-pressure pipelines, and welded flanges for pressures of more than four kilograms. A gasket is added between the two flanges and then tightened with bolts. The thickness of flanges with different pressures is different, and the bolts they use are also different. When water pumps and valves are connected to pipelines, parts of these equipment and equipment are also made into corresponding flange shapes, which are also called flange connections. All connecting parts that are connected by bolts on the periphery of two planes and are closed at the same time are generally called "flanges", such as the connection of ventilation pipes. This type of parts can be called "flange parts". However, this connection is only a part of the equipment, such as the connection between the flange and the water pump, it is not good to call the water pump "flange parts". Smaller ones, such as valves, can be called "flange parts".
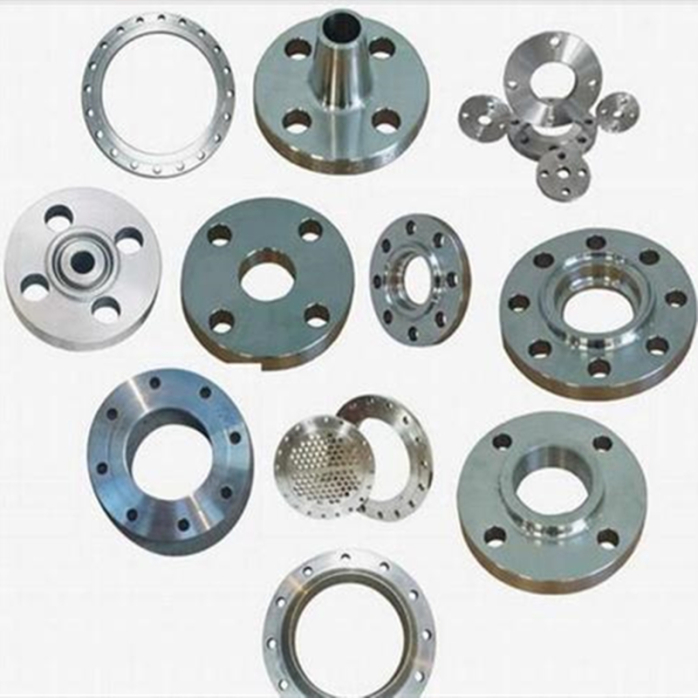
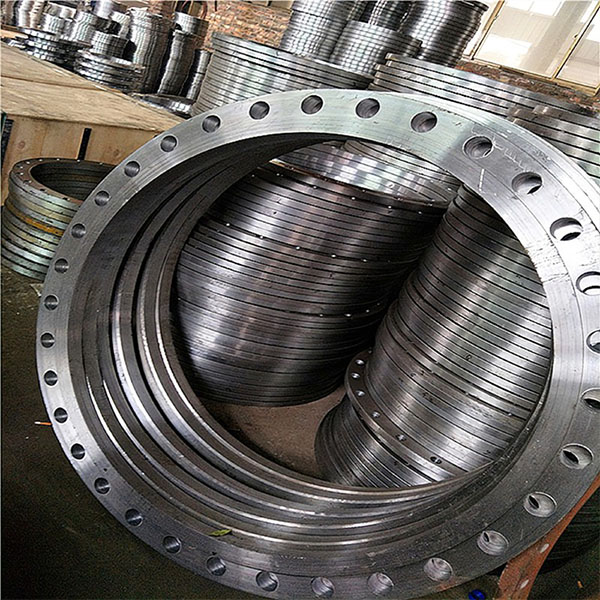
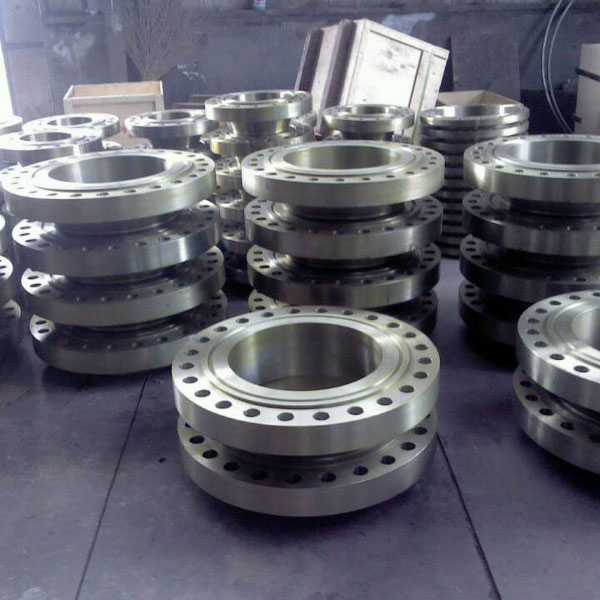
1. According to the chemical industry (HG) industry standards: integral flange (IF), threaded flange (Th), plate flat welding flange (PL), neck butt welding flange (WN), neck flat welding flange (SO), socket welding flange (SW), butt welding ring loose flange (PJ/SE), flat welding ring loose flange (PJ/RJ), lining flange cover (BL(S)), Flange cover (BL).
2. According to the petrochemical (SH) industry standard: threaded flange (PT), butt welding flange (WN), flat welding flange (SO), socket welding flange (SW), loose flange (LJ) , Flange cover (not shown).
3. According to machinery (JB) industry standards: integral flange, butt welding flange, plate flat welding flange, butt welding ring plate loose flange, flat welding ring plate loose flange, flanged ring plate loose flange Flange, flange cover.
4. According to national (GB) standards: integral flanges, threaded flanges, butt welding flanges, neck flat welding flanges, neck socket welding flanges, butt welding ring neck loose flanges, plate flat flanges Welding flanges, butt-welding ring plate loose flanges, flat welding ring plate loose flanges, flanged ring plate loose flanges, flange covers.
WCB (carbon steel), LCB (low temperature carbon steel), LC3 (3.5% nickel steel), WC5 (1.25% chromium 0.5% molybdenum steel), WC9 (2.25% chromium), C5 (5% chromium 0.5% molybdenum), C12 (9% chromium and 1% molybdenum), CA6NM (4 (12% chromium steel), CA15(4) (12% chromium), CF8M (316 stainless steel), CF8C (347 stainless steel), CF8 (304 stainless steel), CF3 (304L) Stainless steel), CF3M (316L stainless steel), CN7M (alloy steel), M35-1 (Monel), N7M (Haast Nickel Alloy B), CW6M (Hasta Nickel Alloy C), CY40 (Inconel) Wait.
The production process is mainly divided into four types: forging, casting, cutting and rolling.
(1) Cast flange and forged flange
The cast flange has accurate shape and size, small processing volume and low cost, but has casting defects (pores, cracks, inclusions); the internal structure of the casting is poor in streamline (if it is a cutting part, the streamline is worse);
Forged flanges generally have lower carbon content than cast flanges and are not easy to rust. Forgings are streamlined, have a denser structure, and have better mechanical properties than cast flanges;
Improper forging process will also cause large or uneven crystal grains, hardening cracks, and forging costs higher than cast flanges.
Forgings can withstand higher shear and tensile forces than castings.
The advantage of castings is that they can produce more complex shapes and lower costs;
The advantage of forgings is that the internal structure is uniform, and there are no harmful defects such as pores and inclusions in the casting;
From the production process, the difference between cast flange and forged flange is different. For example, centrifugal flange is a kind of cast flange.
Centrifugal flanges belong to the precision casting method to produce flanges. Compared with ordinary sand casting, the structure of this type of casting is much finer, and the quality is improved a lot. It is not prone to problems such as loose structure, pores, and trachoma.
First of all, we need to understand how the centrifugal flange is produced, the process method and product of the centrifugal casting to make the flat welding flange, which is characterized in that the product is processed through the following process steps:
① Put the selected raw material steel into an intermediate frequency electric furnace for smelting, so that the temperature of molten steel reaches 1600-1700℃;
② Preheat the metal mold to 800-900℃ to maintain a constant temperature;
③ Start the centrifuge, and pour the molten steel in step ① into the metal mold after preheating in step ②;
④ The casting is naturally cooled to 800-900℃ and kept for 1-10 minutes;
⑤ Cool with water to near normal temperature, demould and take out the casting.