1. Wear-resistant steel plate overview
Wear Resistant Steel Plate, namely wear-resistant steel plate, is a special plate product specially used under large-area wear working conditions. It is composed of low-carbon steel plate and alloy wear-resistant layer.
The wear-resistant steel plate has the characteristics of high strength and high wear resistance. The alloy wear-resistant layer is generally 1/3 to 1/2 of the total thickness. When in work, the matrix provides comprehensive properties such as strength, toughness and plasticity to resist external forces, and the alloy wear-resistant layer provides wear resistance to meet the requirements of specified working conditions.
There are several types of wear-resistant steel plates, including composite wear-resistant steel plates and alloy quenched wear-resistant steel plates. For example, KN60 wear-resistant steel plate is a kind of product made by compounding a certain thickness of alloy wear-resistant layer with high hardness and excellent wear resistance on the surface of ordinary low-carbon steel or low-alloy steel with good toughness and plasticity through surfacing method. The technical parameters of KN60 wear-resistant steel plate are as follows: the Vickers hardness is 1700HV; the material is low-carbon steel base, and other types of surfacing hard alloys and niobium carbide can be provided according to requirements. The chromium and boron alloy carbides are rich; the hardness of the composite wear-resistant layer is C62-65 HRc; the thickness is 3 - 15 millimeters; the hard alloy content is more than 50%; the maximum working temperature is 1000°C.
In addition, wear-resistant steel plate 360 is also a kind of high-strength and high-wear-resistant wear-resistant plate. It is manufactured by prestressing technology and has better tensile strength and compressive strength, as well as good wear resistance and impact resistance.
2. Uses of wear-resistant steel plates
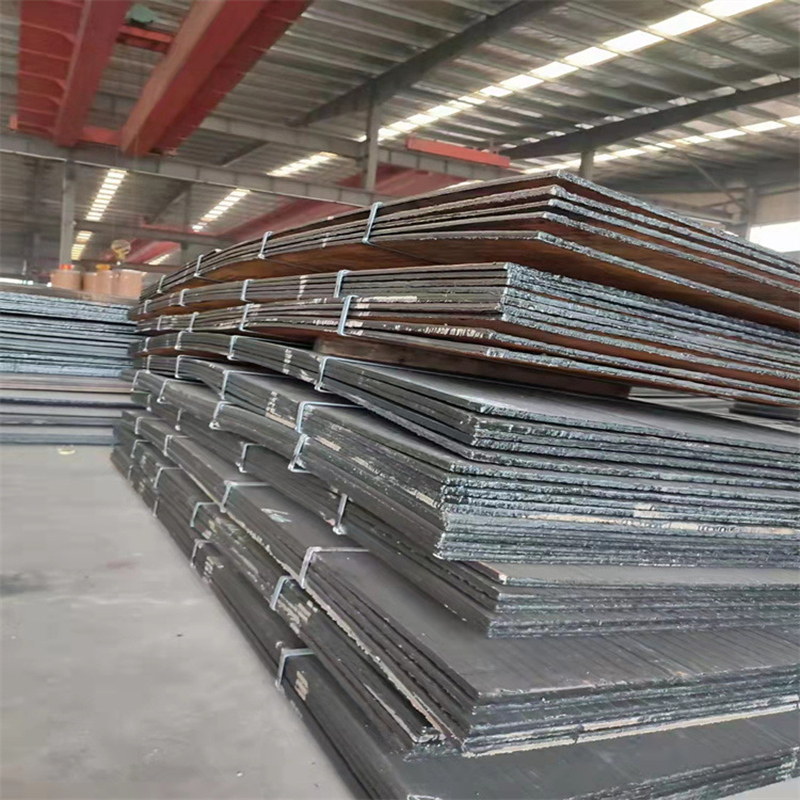
2.1 Wide range of industrial applications
Wear-resistant steel plates find extensive applications in various industries. In the metallurgical industry, they are used in equipment such as crushers and conveyor belts, which are constantly subjected to abrasion and impact. In the coal industry, they are employed in coal chutes and mining machinery parts to withstand the harsh wear conditions. The cement industry makes use of wear-resistant steel plates in kilns and grinding mills to ensure long service life. In the power industry, they are used in coal pulverizers and ash handling systems.
For example, wear-resistant steel plate 360 is widely used in fields such as automobiles, railways, aviation, metallurgy, chemical industry, machinery, petroleum, electricity, water conservancy, and construction. It is ideal for components that bear large impact loads in industrial machinery due to its excellent wear resistance, impact resistance, and corrosion resistance.
2.2 High cost-effectiveness
Compared with other materials, wear-resistant steel plates offer high cost-performance. Although the initial cost of wear-resistant steel plates may be slightly higher than some traditional materials, their superior wear resistance and durability result in significant savings in the long run. For instance, a company using wear-resistant steel plates in its production process may experience reduced downtime for equipment maintenance and replacement, leading to increased productivity and cost savings.
According to data, the service life of wear-resistant steel plates is often several times longer than that of ordinary steel plates. This means that companies can reduce their material costs and maintenance expenses over time. Additionally, the excellent performance of wear-resistant steel plates reduces the risk of equipment failure and production delays, further enhancing their economic benefits. As a result, more and more industries and manufacturers are showing a preference for wear-resistant steel plates.
3. Material classification of wear-resistant steel plates
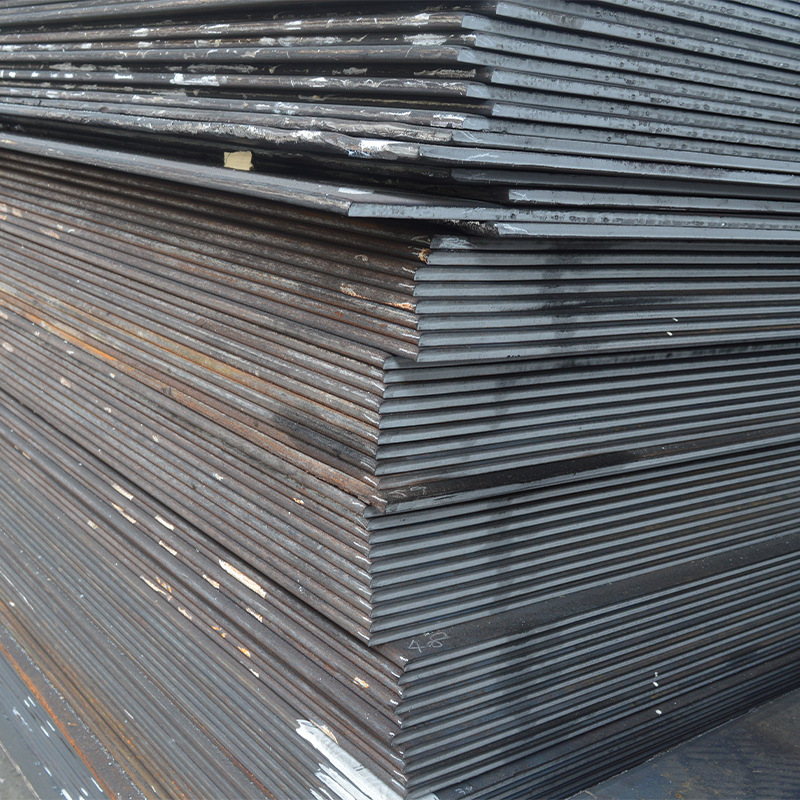
3.1 Common material types
Wear-resistant steel plates are commonly made by surfacing alloy wear-resistant layers on the surface of ordinary low-carbon steel or low-alloy steel. There are also cast wear-resistant steel plates and alloy quenched wear-resistant steel plates. For example, the composite wear-resistant steel plate is made by compounding a certain thickness of alloy wear-resistant layer with high hardness and excellent wear resistance on the base metal.
3.2 Different types of characteristics
There are mainly three types of wear-resistant steel plates: general-purpose type, impact-resistant type, and high-temperature resistant type.
The general-purpose wear-resistant steel plate has stable performance and is suitable for general wear conditions. It has good wear resistance and moderate strength. The technical parameters might include a certain hardness level, typically around 50-60 HRC. The material composition usually contains elements such as chromium and manganese to enhance wear resistance. In performance, it can withstand a certain degree of abrasion and is widely used in industries such as machinery manufacturing.
The impact-resistant wear-resistant steel plate is designed to withstand heavy impacts. It has high toughness and excellent impact resistance. The material often contains alloy elements that enhance its impact resistance. For example, some impact-resistant wear-resistant steel plates may have a hardness of around 45-55 HRC but with superior impact resistance. This type is suitable for applications where equipment is subject to frequent impacts, such as in the mining and construction industries.
The high-temperature resistant wear-resistant steel plate can withstand high temperatures. It is made of special alloy materials that can maintain stability at high temperatures. The technical parameters might include a maximum operating temperature of up to 800-1200°C. The material composition usually contains elements such as nickel and chromium to ensure high-temperature resistance. In performance, it is widely used in high-temperature environments such as furnaces and kilns in the metallurgical and cement industries.
Post time: Oct-31-2024