Hot Rolled Alloy Water Tank Container Used Steel Boiler Plate A516-70
Q460 is a high-strength low-alloy steel. Q460's designation method: its steel number is prefixed with "Q", which represents the yield point of the steel, that is, the yield strength. The following number indicates that the yield point value 460 represents 460 MPa, mega is the 6th power of 10, and Pa is the pressure unit Pascal. Q460 means that the plastic deformation of steel will only occur when the strength of the steel reaches 460 MPa, that is, when the external force is released, the steel can only maintain the stressed shape and cannot return to its original shape. This strength is greater than that of ordinary steel. The general quality grade symbols are A, B, C, D, E, respectively. On the basis of ensuring low carbon equivalent, Q460 appropriately increases the content of microalloying elements. Good welding performance requires a low carbon equivalent of steel, and the increase of microalloying elements increases the strength of the steel while also increasing the carbon equivalent of the steel. But fortunately, the added carbon equivalent is small, so it will not affect the welding performance of the steel.
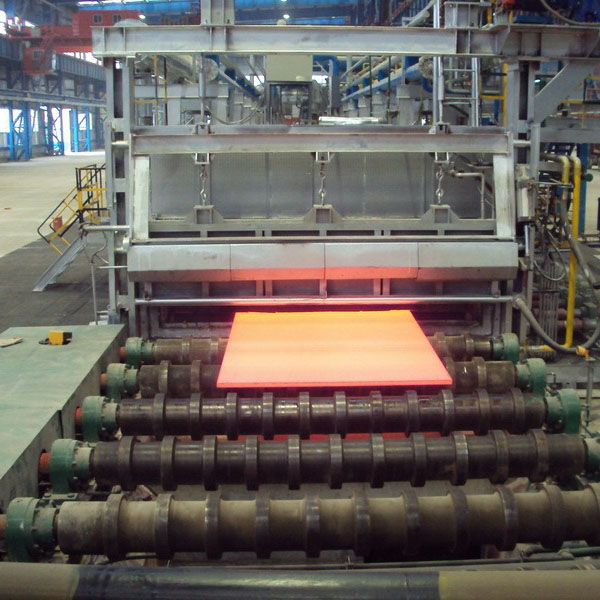
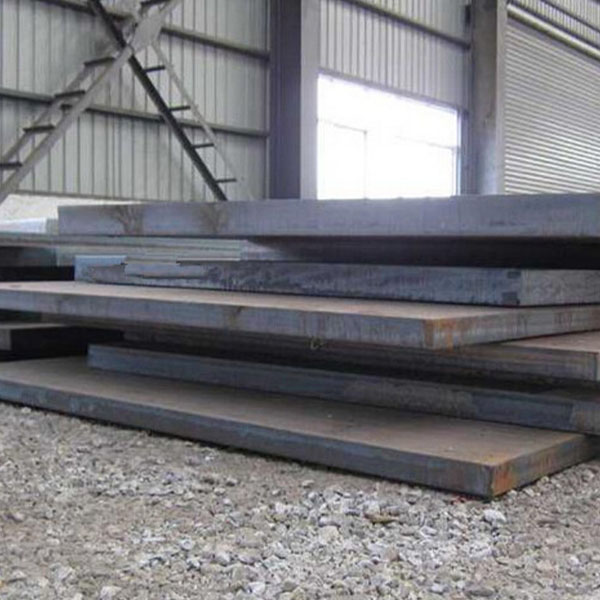
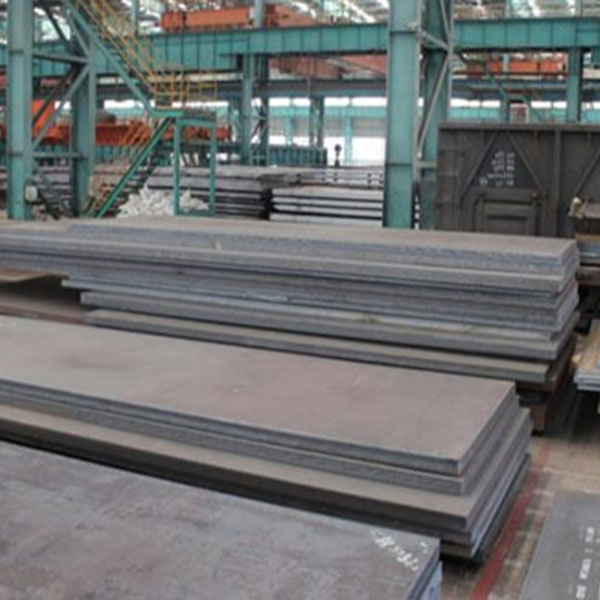
The rapid development of automobile industry has played an important role in national economic and social development. However, due to the impact of energy shortage, environmental pollution and other problems, the contradiction in the development of the industry has become increasingly prominent. Looking forward to the future, the development of the industry can only be sustainable if it is based on the background of nature, ecology, energy conservation and safety.
Under this background, the application of automobile lightweight and high strength steel has become an important development direction. However, with the improvement of the strength of high-strength steel plate, the traditional cold stamping process is prone to fracture in the forming process, which can not meet the processing requirements of high-strength steel plate. In this case, the hot stamping forming technology of ultra-high strength steel plate has been gradually studied in the world - a new process integrating forming, heat transfer and microstructure transformation, which mainly uses the characteristics of increased plasticity and reduced yield strength of sheet metal in the state of high temperature austenite. However, thermoforming requires in-depth research on process conditions, metal phase transformation and CAE analysis technology, but this technology is monopolized by foreign manufacturers and develops slowly in China.
According to the survey and statistics, the application of high-strength steel of some automobile brands is expanding, and the application of high-strength steel of body frame of some models has reached 90%. According to the research of the energy department of the American Iron and Steel Institute, even if the value of high-strength steel is reduced, its tension is much more difficult than the traditional cold plate. The ductility of high-strength steel is only half that of ordinary steel.
When the material is formed by stamping, it will harden. Different steels have different degrees of hardening. Generally, high strength low alloy steel only increases slightly by 20MPa, less than 10%. Note: the yield strength of dual phase steel increased by 140 MPa, an increase of more than 40%! During the forming process, the metal will become completely different, completely unlike before the stamping process begins. The yield strength of these steels increases a lot after being stressed. The higher yield stress of the material coupled with work hardening is equal to a significant increase in flow stress. Therefore, cracking, springback, wrinkling, workpiece size, die wear and micro welding wear have become the focus of problems in the forming process of high strength steel.
Based on the characteristics and characteristics of high strength steel, if the metal flow can not be changed and friction can not be reduced, the cracking and uneven texture of high strength steel (HSS) may lead to the increase of component scrap rate. The high kilopound force per square inch (Ksi) of this material (the unit for measuring yield force), enhanced rebound, work hardening tendency and operation at elevated forming temperature are all challenges for the die.
Laser tailor-welded blank and continuous variable cross-section board technology
1. Tailor Welded Blanks (Tailor Welded Blanks, TWB) uses laser as the welding heat source to combine and weld several different materials, different thicknesses, and different coatings of steel, stainless steel, aluminum alloy, etc. into a whole plate.
2. Using laser tailored welding technology, it is possible to reasonably combine materials of different thickness sizes and strength levels according to the stress conditions of the structural parts, improve the structural rigidity while reducing the weight of the parts, and also increase the utilization rate of materials and reduce the number of parts. The number of parts in the simplifies the process. Laser tailored welding technology has become the main technical means of automobile lightweight, and it has been applied to the models of many manufacturers. Mainly used in front and rear door inner panels, front and rear longitudinal beams, side panels, floor panels, A, B, and C pillars on the inside of the door, wheel covers and trunk inner panels, etc.
3. Tailor Rolling Blanks (TRB), also called differential thickness plates, refers to the real-time change of the roll gap size through the computer during the rolling process of the steel plate, so that the rolled thin plate has a pre-determined direction along the rolling direction. Custom variable cross-sectional shape.
4. Continuous variable cross-section panel technology has been widely used in the manufacture of body structure parts, such as engine cover, B-pillar, body chassis, motor spacer guide, middle column inner panel, mudguard and crash box, etc., and has been successfully applied to Audi, BMW, Volkswagen, GM and other models.
5. Laser tailored welding and continuous variable cross-section technology change the thickness of the stamping material through different technological means, and are used to solve the problem of different load-bearing capacity requirements for different parts of auto parts under load. Compared with the two, the advantage of tailor-made laser welding technology lies in its flexibility, which can realize the splicing of any position and the splicing of different materials. The advantage of continuous variable cross-section technology is that there is no welding seam, the hardness change along the length direction is relatively gentle, it has better formability, and the surface quality is good, the production efficiency is high, and the cost is low. Luggage, medical equipment, motorcycle shell; automobile, bus inner roof, dashboard; seat backing, door panel, window frame, etc.
Product Name |
Hot Rolled Alloy Water Tank Container Used Steel Boiler Plate a516-70 |
Standard |
Astm, Gb, Din, Jis, En, Etc. |
Material |
Boiler Steel |
Size |
Thickness: 2-300mm |
Width: 1000-3000mm |
|
Length: 1000~12000mm Or As Required |
|
Application |
Building Construction, Bridges, Vehicle Parts, Buttocks, High-Pressure Vessels, Boilers, Large Structural Steels, Etc. |
Delivery Status |
Hot Rolling, Controlled Rolling, Normalizing Or As Required |
Surface |
Hic, Ssc, Spwht, As Required |
Certification |
Bv、Iso、Sgs、Ce ... |
To Pay |
t/t, l/c, West Union, Etc. |
Delivery Time |
15-20 Days After Deposit, Depending On Quantity |
Pack |
Standard Shipping Package Or As Required |