Galvanized Welded Pipe
In order to improve the corrosion resistance of steel pipes, general steel pipes are galvanized. Galvanized steel pipes are divided into two types: hot-dip galvanizing and electro-galvanizing. The hot-dip galvanizing layer is thick, the cost of electro-galvanizing is low, and the surface is not very smooth.
Oxygen-blowing welded pipe: Used as a steel-making oxygen-blowing pipe, generally small-diameter welded steel pipes, with eight specifications ranging from 3/8 to 2 inches. It is made of 08, 10, 15, 20 or 195-Q235 steel strip, in order to prevent corrosion, it is necessary to carry out aluminizing treatment.
Most old houses use galvanized pipes. The iron pipes used for gas and heating are also galvanized pipes. Galvanized pipes are used as water pipes. After a few years of use, a lot of rust and dirt are generated in the pipes, and the yellow water that flows out not only pollutes the sanitary ware. , And mixed with bacteria that breed on the uneven inner wall, rust causes excessive heavy metal content in the water, which seriously endangers human health. In the 1960s and 1970s, developed countries in the world began to develop new types of pipes and gradually banned galvanized pipes. Four ministries and commissions including the Ministry of Construction of China also issued a document clarifying that galvanized pipes have been banned from 2000 onwards. Galvanized pipes are rarely used for cold water pipes in newly built communities after 2000, and galvanized pipes are used for hot water pipes in some communities.
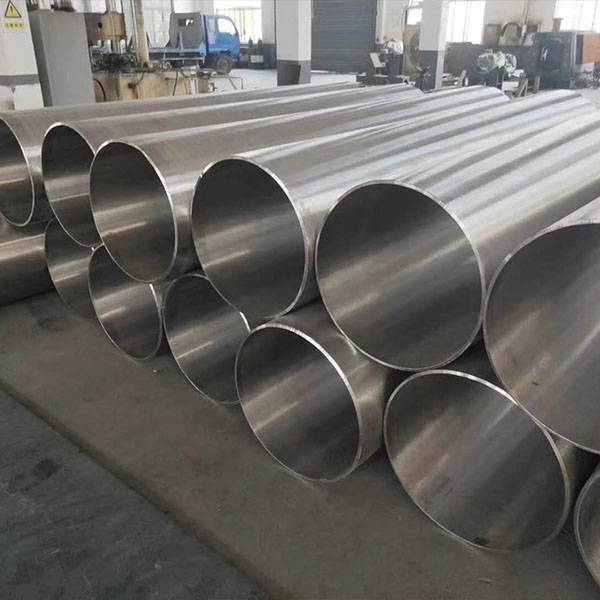
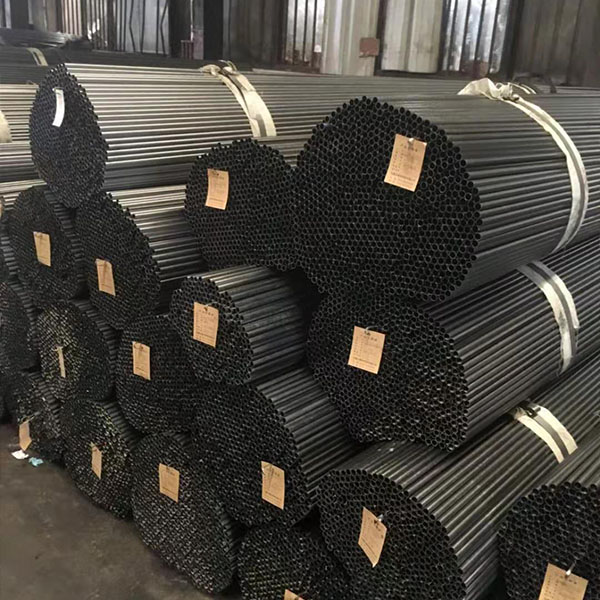
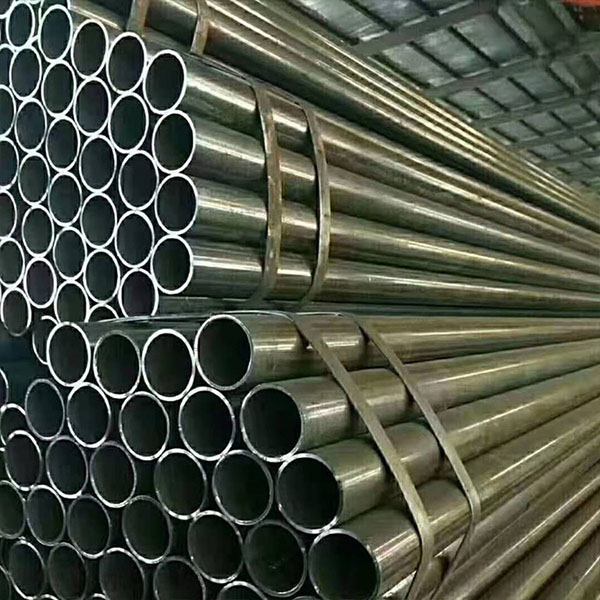
Nominal wall thickness mm 2.0 2.5 2.8 3.2 3.5 3.8 4.0 4.5
Galvanized steel pipes are divided into cold galvanized pipes and hot-dip galvanized pipes. The former has been banned, and the latter has been promoted by the state to be temporarily usable.
Hot-dip galvanized pipe
The hot-dip galvanized pipe is to make the molten metal and the iron matrix react to produce an alloy layer, so that the matrix and the coating are combined. Hot-dip galvanizing is to pickle the steel pipe first. In order to remove the iron oxide on the surface of the steel pipe, after the pickling, it is cleaned in a tank of ammonium chloride or zinc chloride aqueous solution or a mixed aqueous solution of ammonium chloride and zinc chloride, and then sent to In the hot dip plating tank. Hot-dip galvanizing has the advantages of uniform coating, strong adhesion and long service life.
Cold galvanized pipe
Cold galvanizing is electro-galvanizing, and the amount of galvanizing is very small, only 10-50g/m2, and its corrosion resistance is much worse than that of hot-dip galvanized pipes. Most of the regular galvanized pipe manufacturers do not use electro-galvanized (cold plating) in order to ensure the quality. Only those small enterprises with small scale and outdated equipment use electro-galvanization, and of course their prices are relatively cheaper. The Ministry of Construction has officially announced that cold-galvanized pipes with outdated technology should be eliminated, and cold-galvanized pipes will not be allowed to be used as water and gas pipes in the future.
Hot-dip galvanized steel pipe: The steel pipe matrix undergoes a complex physical and chemical reaction with the molten plating solution to form a corrosion-resistant zinc-iron alloy layer with a compact structure. The alloy layer is integrated with the pure zinc layer and the steel pipe matrix. Therefore, its corrosion resistance is strong.
Cold galvanized steel pipe: The zinc layer is an electroplated layer, and the zinc layer and the steel pipe substrate are layered independently. The zinc layer is thin, and the zinc layer simply adheres to the steel pipe substrate and is easy to fall off. Therefore, its corrosion resistance is poor. In newly-built houses, it is forbidden to use cold galvanized steel pipes as water supply pipes.
The production process of stainless steel has the following production steps:
a. Round steel preparation; b. Heating; c. Hot rolled piercing; d. Cut the head; e. Pickling; f. Grinding; g. Lubrication; h. Cold rolling processing; i. Degreasing; j. Solution heat treatment; k. Straightening; l. Cut the tube; m. Pickling; n. Product testing.
Only provide the general process, and the more detailed ones belong to the secrets of each manufacturer
1. Brand and chemical composition
The grade and chemical composition of the steel for galvanized steel pipes should comply with the grade and chemical composition of the steel for black pipes specified in GB 3092.
2. Manufacturing method
The manufacturing method of the black pipe (furnace welding or electric welding) is selected by the manufacturer. Hot-dip galvanizing is used for galvanizing.
3. Thread and pipe joints
3.1 For galvanized steel pipes delivered with threads, the threads should be machined after galvanizing. The thread should comply with YB 822 regulations.
3.2 Steel pipe joints should comply with YB 238; malleable cast iron pipe joints should comply with YB 230.
4. Mechanical properties The mechanical properties of steel pipes before galvanizing should meet the requirements of GB 3092.
5. The uniformity of the galvanized layer Galvanized steel pipe should be tested for the uniformity of the galvanized layer. The steel pipe sample shall not turn red (copper-plated color) after being immersed in copper sulfate solution for 5 consecutive times.
6. Cold bend test The galvanized steel pipe with a nominal diameter of not more than 50mm should be subjected to a cold bend test. The bending angle is 90°, and the bending radius is 8 times the outer diameter. There is no filler during the test, and the weld of the sample should be placed on the outside or upper part of the bending direction. After the test, there should be no cracks and peeling of the zinc layer on the sample.
7. Water pressure test The water pressure test should be carried out in the clarinet. Eddy current flaw detection can also be used instead of the water pressure test. The test pressure or the size of the comparison sample for eddy current testing shall meet the requirements of GB 3092.