Carbon Steel Boiler Plate
steel plate(s) for bridges
The bridge slab is a thick steel plate dedicated to the manufacture of bridge structural parts. It is made of carbon steel and low-alloy steel for bridge construction with special steel grades. The end of the steel number is marked with the word q (bridge). Carbon steel for bridge construction includes A3q for riveting bridge structures and 16q for welding bridge structures; low-alloy steel for bridge structures includes 12Mnq, 12MnVq, 15MnVNq, 16Mnq, etc. The thickness of the bridge steel plate is 4.5-50 mm.
Application areas:
Road bridges and railway bridges used to make riveted and bolt-welded structures, including cross-sea bridges, etc.
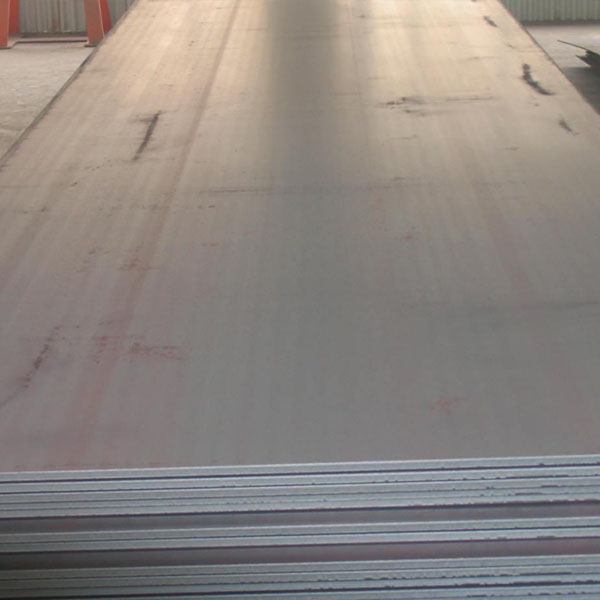
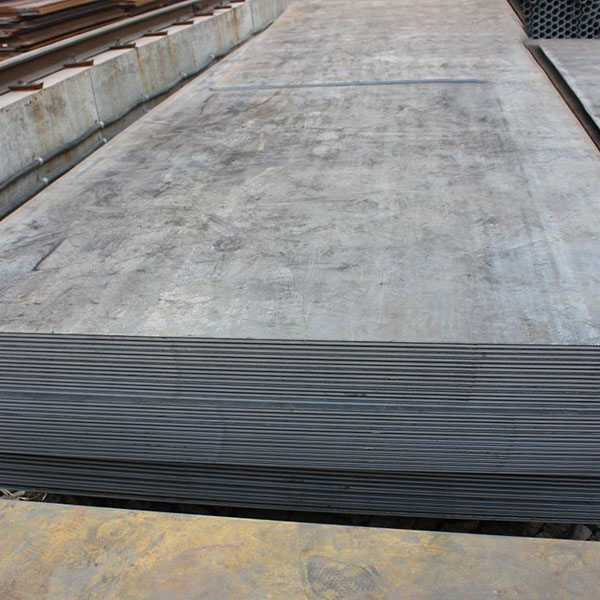
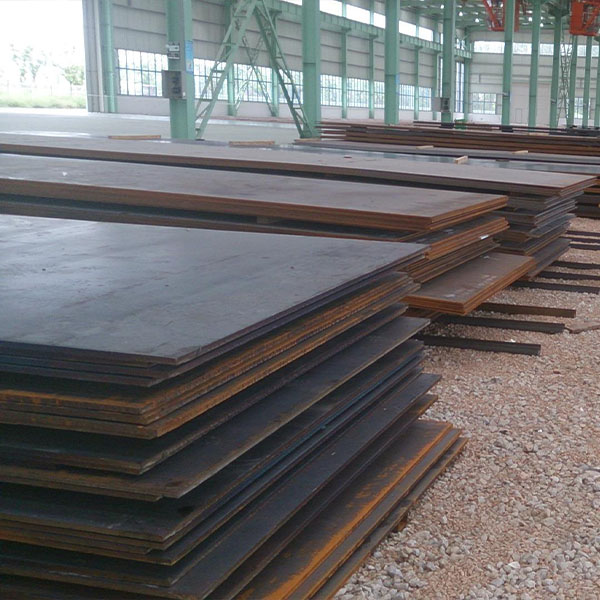
Steel plate for bridge | Grade | Executive standard | Remark |
16q, 16Mnq, 16MnCuq15MnVq, 15MnVNq14MnNbp, Q345q, Q420q A709M (Gr36, 50, 50W, 70W) | YB168 and YB(T) 10GB/ T714ASTM | 1. Can produce Z15-Z35 various grades of anti-lamellar tearing (thickness direction performance) steel plates. 2. Production specifications: thickness 8mm-400mm, width 1500mm-3900mm, length 3000mm-18000mm. The two parties agreed to supply steel plates of larger specifications. 3. According to the performance and user needs, the delivery status of the steel plate can be hot rolled, controlled rolling, normalized, and annealed |
Laser tailor-welded blank and continuous variable cross-section board technology
1. Tailor Welded Blanks (Tailor Welded Blanks, TWB) uses laser as the welding heat source to combine and weld several different materials, different thicknesses, and different coatings of steel, stainless steel, aluminum alloy, etc. into a whole plate.
2. Using laser tailored welding technology, it is possible to reasonably combine materials of different thickness sizes and strength levels according to the stress conditions of the structural parts, improve the structural rigidity while reducing the weight of the parts, and also increase the utilization rate of materials and reduce the number of parts. The number of parts in the simplifies the process. Laser tailored welding technology has become the main technical means of automobile lightweight, and it has been applied to the models of many manufacturers. Mainly used in front and rear door inner panels, front and rear longitudinal beams, side panels, floor panels, A, B, and C pillars on the inside of the door, wheel covers and trunk inner panels, etc.
3. Tailor Rolling Blanks (TRB), also called differential thickness plates, refers to the real-time change of the roll gap size through the computer during the rolling process of the steel plate, so that the rolled thin plate has a pre-determined direction along the rolling direction. Custom variable cross-sectional shape.
4. Continuous variable cross-section panel technology has been widely used in the manufacture of body structure parts, such as engine cover, B-pillar, body chassis, motor spacer guide, middle column inner panel, mudguard and crash box, etc., and has been successfully applied to Audi, BMW, Volkswagen, GM and other models.
5. Laser tailored welding and continuous variable cross-section technology change the thickness of the stamping material through different technological means, and are used to solve the problem of different load-bearing capacity requirements for different parts of auto parts under load. Compared with the two, the advantage of tailor-made laser welding technology lies in its flexibility, which can realize the splicing of any position and the splicing of different materials. The advantage of continuous variable cross-section technology is that there is no welding seam, the hardness change along the length direction is relatively gentle, it has better formability, and the surface quality is good, the production efficiency is high, and the cost is low. Luggage, medical equipment, motorcycle shell; automobile, bus inner roof, dashboard; seat backing, door panel, window frame, etc.